In the helicopter the rotor blades are, in effect, long rotating wings of small chord. The blades are mounted on an engine-driven shaft. As they move through the air, they generate lift in the same way as a fixed wing. The obvious advantage over a fixed-wing aircraft is that the rest of the aircraft does not need to move relative to the air, and it can therefore hover.
The torque reaction of the motor tends to rotate the fuselage in the opposite direction to that of the rotor, and on a conventional single rotor helicopter, a tail mounted propeller or fan is used to counteract this effect. The tail propeller, which is normally referred to as the tail rotor, wastes power, and is one cause of the poor efficiency of simple helicopters. A recent innovation is the so-called no-tail rotor (NOTAR) design in which the tail rotor is replaced by a jet of air which interacts with the main rotor downflow to produce the required torque. The NOTAR configuration has a number of operational advantages including reduced noise.
When two rotors are used, they can be arranged to rotate in opposite directions, thus cancelling out the unwanted torque reaction, and removing the need for a tail rotor. The two rotors are normally arranged at opposite ends of the fuselage, but sometimes, particularly in Russian designs, they may be arranged so as to counter-rotate on concentric shafts as illustrated in Fig. 1.25. The use of two rotors considerably increases the cost and complexity of the aircraft. There are also problems due to interference between the two rotor wakes.
On a simple single rotor helicopter, direct control of the amount of lift generated by the main rotor blades is provided by the collective pitch mechanism which changes the incidence or ‘pitch angle’ of all of the blades by the same amount simultaneously. In addition, a cyclic pitch mechanism is provided. This causes the incidence of the blades to increase and decrease once per cycle. The cyclic pitch control is used to control both the nose-up (or nose-down) attitude of the helicopter, and the roll motion about the longitudinal axis. The small tail rotor is also provided with a mechanism which can be used to vary the incidence of its blades, thus altering the amount of thrust produced. This allows it to be used to yaw the aircraft.
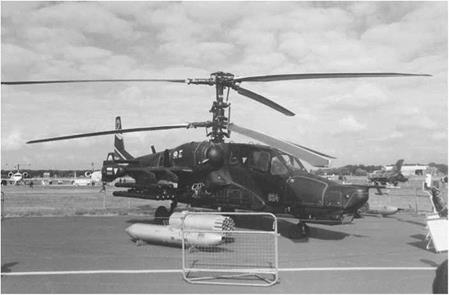
Fig. 1.25 A pair of co-axial counter-rotating rotor blades removes the need for a tail rotor on this Kamov Ka-50. Note the considerable complexity of the rotor heads however
|
On conventional helicopters, particularly older designs, the rotor blades are hinged about two axes at the point where they are joined to the hub, in such a way that they are free both to swing back and forth, and to flap up and down (within limits). The swinging motion is primarily intended to damp out cyclic variations in drag, and this hinge is called the drag (or lag) hinge. A damper is fitted to prevent unwanted oscillations. The flapping motion is resisted by strong centripetal forces, which tend to keep the blades nearly at right angles to the axis of rotation. The lift forces on the blades are always very much smaller than the centripetal forces, but they nevertheless pull the blades up slightly, so that in flight, their rotational path describes a very shallow cone rather than a flat disc.
When the cyclic pitch control is used to vary the incidence cyclically, the blades will tend to flap up and down cyclically in response to the lift variation. If the blades are caused to flap up at the rear, as shown in Fig. 1.27, the effect is to tilt the axis of tip rotation forwards. This generates a horizontal thrust force component, as illustrated, and the helicopter is thus propelled forwards. The flapping hinges are normally offset from the centre of the hub axis, and as the axis of blade rotation is inclined relative to the shaft axis, the centripetal forces produce moments which tend to tilt the rotor axis (and hence the whole aircraft) nose-down. By suitably adjusting the cyclic pitch control, the horizontal propulsion force can be arranged to occur in any desired direction, not just forwards, and it is thus possible to fly a helicopter sideways or backwards.
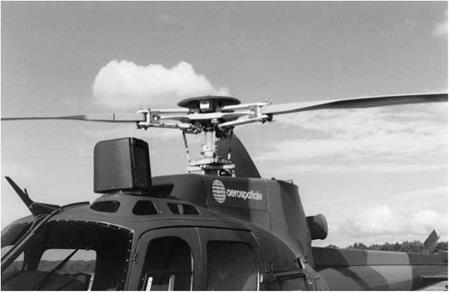
Fig. 1.26 On the so-called rigid rotor design, flapping is provided by flexible members and compliant joints which replace the hinges of older designs. Note the compactness and simplicity relative to the Kamov design shown in Fig. 1.25
|
Fig. 1.27 Helicopter in forward flight
The blades are caused to flap up at the rear by use of the cyclic pitch control. The resultant force provides both lift and thrust components
When a helicopter flies forwards, the relative air speed on the advancing blade side will be greater than on the retreating side. If no corrective action were taken, this would cause the blades to flap up towards the front and down towards the rear, thereby tilting the axis of the blade rotation backwards: a condition known as blowback. If this were allowed to happen unchecked, the helicopter would simply slow down due to the now rearward thrust component. This tendency therefore has to be overcome by making use of the cyclic pitch control to reduce the blade angle of attack when advancing, and increase it when retreating. By this means, the lift is equalised on the advancing and retreating sides. If simple rigidly fixed blades were used, as on a propeller, the blades would generate more lift when advancing than when retreating, and the aircraft would tend to roll.
Two-bladed rotors may use a teetering rotor instead of flapping hinges. In this arrangement, the two blades are rigidly connected together, but allowed to tilt about the hub to produce a flapping motion. A teetering rotor is used on the autogyro shown in Fig. 1.31.
Some more recent helicopter designs do not use hinged blades, but rely on carefully controlled flexure of the mounting points: an arrangement that is often misleadingly referred to as a rigid rotor. Figure 1.26 shows a ‘rigid rotor’ head mechanism. Its relative simplicity and compactness may be contrasted with the great complexity of the conventionally-hinged double unit of the Kamov shown in Fig. 1.25.
The rotor head contains not only the hinges or flexures but must also carry the mechanism for the cyclic and collective pitch control of the blades. This unit is thus a very complicated and heavily loaded item, and almost any mechanical failure is likely to be disastrous. The safety record of helicopters is generally inferior to that of fixed-wing aircraft.
It should be noted that the description above applies to conventional helicopters. Various alternative rotor mechanisms have been tried, including ones with tilting shafts.
Since the rotor provides thrust, lift and the primary means of control, the helicopter can be seen as a good example of a radical departure from Cayley’s classical aeroplane, where each component serves only one specific purpose.
The helicopter also suffers from other problems stemming from the differences in the relative airflow velocities on the advancing and retreating blades. In order for the retreating blade to generate any lift at all, it must be moving faster than the relative airflow. As you can see from Fig. 1.28, this means that the advancing blade must be moving through the air at more than twice the speed of the aircraft. The advancing blade will, therefore, approach the speed of sound, when the aircraft is still only travelling at well below half this speed. Having a blade that continually moves in and out of supersonic flow produces considerable structural and aerodynamic problems, not the least of which is the noise created.
Figure 1.28 also shows a common situation, where the inboard part of the retreating blade is not moving fast enough to overtake the air flow. The
Resultant
Resultant relative velocity
Fig. 1.28 Relative air flow velocities in forward flight air therefore actually flows backwards relative to the blade on this portion. These factors severely limit the maximum speed of conventional helicopters. Figure 1.29 shows the Westland Lynx, which achieved a record-breaking 249.10 mph in 1986. This is less than half the speed attained by the fastest propeller-driven conventional aircraft.
A complete description of helicopter aerodynamics is beyond the scope of this book, but the above outline gives some idea of why rotating wing aircraft have not displaced fixed wing types, despite the obvious attraction of vertical take-off and landing.