Any hinged control surface on a model may flutter. Flutter is an oscillation or violent shaking to and fro of the control surface, and it may set off sympathetic flutter in the wings or tail, or in other hinged members. In some cases, such flutter may be mild and almost harmless. The control surface affected vibrates slightly at certain airspeeds, possibly emitting an audible buzzing, but the oscillation does not build up and ceases as soon as the air speed drops. In other cases the flutter builds up rapidly and the model becomes uncontrollable, sheds control surfaces, or breaks up, with very little warning. The operator may have no idea what happened. The incident may be blamed on radio interference, or lack of structural strength.
 |
In a simple case of flutter, the first cause is the inertia of the control surface itself. The effect may be simulated in an elementary way if a model fuselage with a hinged rudder disconnected from its control rod, is shaken from side to side violently. As the rear end of the fuselage moves, then reaches the end of its ‘shake’ and starts in the other direction, the hinged surface tends to bang over against its stops. It then follows the fuselage through the next movement, and when the fuselage stops moving to begin its return swing, the control surface bangs against the stops again in the other direction. When the model is flying, it is evident that such a control movement may be in phase with the oscillation of the fuselage. A rudder movement by the pilot, or a gust, causes the rear end of the model to swing. The rudder goes with this swing but when the fuselage stops, the rudder’s mass carries it further, which applies aerodynamic force tending to start the fuselage on its return swing. At the end of this second movement, the fuselage again stops and begins to swing back, but the rudder carries on, and again helps to push the fuselage on its way. At some critical airspeed the result will be a continuing oscillation, the rudder will bang violently from side to side and the fuselage with it Something, usually the rudder itself, will break if this
continues. Flutter of an elevator begins in the same fashion, and can be more dangerous since loss of the elevator control is usually disastrous for the model. Aileron flutter is even more common. Since wings are usually flexible, and ailerons large and relatively heavy, flutter is quite probable, especially at high speeds. Wings without ailerons, if too flexible in torsion, will also flutter at high speeds, the tip sections twisting to and fro almost as if they were hinged to the stiffer inboard panels. The twisting changes the angle of attack causing the wings to bend up and down rapidly.
Modellers who have never seen genuine wing flutter sometimes mistakenly refer to the normal up and down bending of wings under varying loads as flutter. Any wing will flex and must do so in flight Flutter of a wing is a rapid, rhythmic oscillation with simultaneous twisting. It is unmistakable, and, once started, hard to stop.
The case of the lightweight wing which flutters often arises when a model is based on an earlier free flight design, which was successful when trimmed for slow flight. Fitted with radio and controlled by rudder and elevator, the model may develop wing flutter when flown at speeds for which its wing was never really intended. In such cases the solution is to stiffen the structure.
If the torsional axis of the wing, i. e. the line around which the outer panels twist, lies ahead of the wing’s centre of gravity, flutter is sure to occur at some speed. The stiffening should be added to the leading edge, usually in the form of sheet balsa covering and vertical spar webbing, to produce a ‘D’ shaped torsion tube. The extra weight added near the leading edge also helps to bring the centre of gravity nearer to the torsional ‘hinge’ line. This is in effect a partial mass balance. Other forms of stiffening, such as diagonal ribs, or (as in some older types of wooden full-sized aircraft) by twin spars with diagonal strutting internally between the spars, is less effective because it does not move the centre of gravity of the structural members forward.
To prevent flutter it is essential for the hinged surfaces, especially on fast models, to be without slop, and for the wings and fuselage to be stiff. Stiffness is not the same thing as
Fig. 13.9 Wing flutter
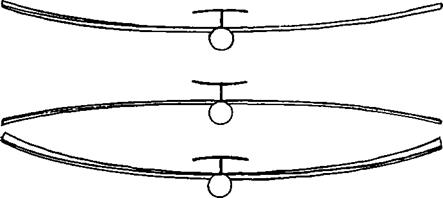
|

|
strength. A fibre glass rod or arrow shaft is very strong, but is not very stiff, indeed the flexibility of glass combined with strength is its main recommendation to archers who use it for bows as well as arrows. Some sailplane models, like their full-sized counterparts, with slender fibreglass fuselages, are inviting tail flutter at high speeds. Secondly, the control rods and cables, and all their linkages, should be free from ‘play’ and again, as stiff as possible. This does not necessarily mean the pivots should be hard to move (although this, too, will help to prevent flutter), but the control rods themselves should not be easily flexed or bent by end loads. In models this is far from easy to arrange, but in general wooden push rods of adequate strength are usually stiff enough, whereas stranded cables, nylon ‘snake’ tubes, etc. are less so. Tubular metal (light alloy) arrow shafts are probably best of all, but costly. Finally, the control surfaces themselves should be as lightly built and as stiff as possible, and, where possible, mass-balanced. It is the mass of the control surface itself that is primarily responsible for flutter and it follows that if the mass can be reduced, flutter is less likely. However, if the control can be balanced so that its centre of mass, or centre of gravity, is ahead of the hinge line, the inertia of the balanced surface will prevent flutter altogether. Repeating the experiment with a rudder on a model fuselage, if the mass balancing is correctly done, the rudder will always be opposed to the fuselage oscillation, however violent